سبد خرید خالی است.
بازگشت به فروشگاه- بلاگ
- Uncategorized @fa
- روش های ساخت محصولات پلاستیکی
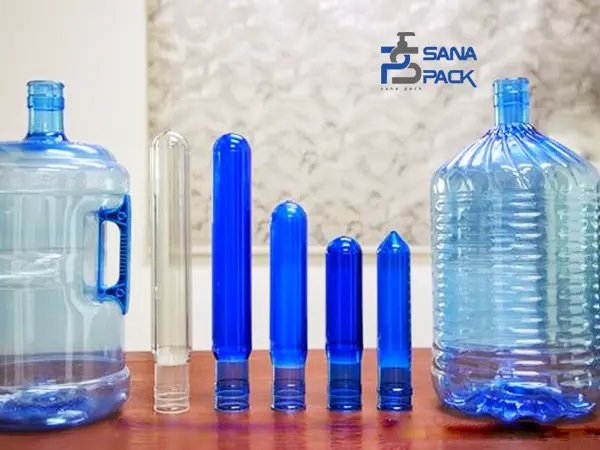
07اکتبر
ساخت محصولات پلاستیکی
ساخت محصولات پلاستیکی میتواند با استفاده از چند روش مختلف صورت گیرد. هر یک از این ها برای نوع مختلف محصول، مقیاس تولید و مواد متفاوت مورد استفاده مناسب هستند. در زیر، به برخی از روشهای اصلی ساخت محصولات پلاستیکی اشاره میکنم:
قالب گیری تزریقی پلاستیک(Plastic Injection Molding)
قالبگیری تزریقی پلاستیک یک فرآیند تولید صنعتی است که در آن مواد پلاستیکی مایع به وسیله یک دستگاه قالبگیری به داخل حفره یا قالبی مخصوص تزریق میشوند. سپس این ماده پلاستیکی تحت فشار و در دمای مناسب به داخل قالب تزریق میشود و شکل سطح داخلی قالب را به خود میگیرد.
بعد از تزریق، ماده پلاستیکی سرعتاً سرد و جامد میشود. در این مرحله، قالب شکلدهی باز میشود و قطعه پلاستیکی تازه تولید شده از داخل قالب خارج میشود.
این روند به صورت تکراری برای تولید تعداد زیادی از قطعات پلاستیکی یکسان یا متغیر انجام میشود. این متد به دلیل سرعت و کارآیی بالا به میزان گستردهای در صنایع مختلف استفاده می شود. تولید پریفرم، صنعت بستهبندی خودروسازی، الکترونیک، اسباببازیها، و پزشکی نمونه هایی از این صنایع هستند.
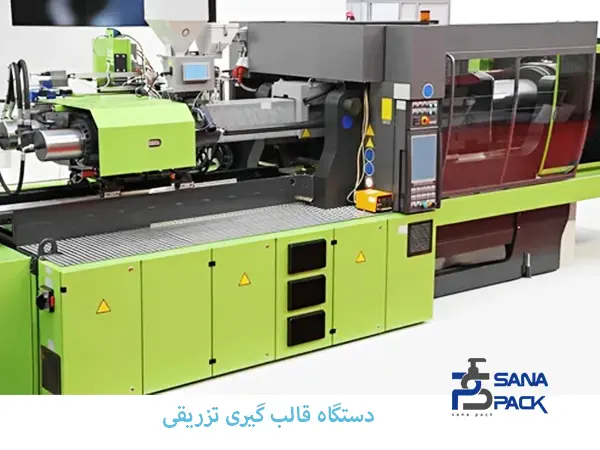
مزایا و معایب قالب گیری تزریقی پلاستیکی
مزایا:
تولید با حجم بالا
سطح دقت عالی
مقاومت و استحکام
کاهش هدررفت مواد مصرفی
معایب:
هزینه قالبسازی
پیچیدگی در طراحی قالب
محدودیتهای دسترسی به مواد مصرفی
در کل، قالبگیری تزریق پلاستیک یک متد تولید مهم و متنوع پلاستیک است که با توجه به مزایا و معایب آن، برای تولید محصولات مختلف در صنایع مختلف مورد استفاده قرار میگیرد. اما برای بهینهسازی این پروسه، نیاز به طراحی دقیق قالب و انتخاب مواد مناسب دارید.
قالب گیری چرخشی (Rotational (Roto) Molding)
قالبگیری چرخشی یک روش تولید قطعات پلاستیکی است که از یک سازوکار خاص برای ایجاد اشکال مختلف از مواد پلاستیکی استفاده میکند. این فرآیند از یک ابزار به نام قالب تشکیل شده است که دو بخش اصلی به نام هسته و حفره دارد. با این حال، این متد با قالبگیری تزریقی تفاوتهای مهمی دارد. سازوکار قالب گیری چرخشی به شرح زیر است:
در ابتدا، پودر پلاستیک به دقت در حفره قالب قرار میگیرد و سپس قالب به یک فر گرم انتقال داده میشود. در حین انجام این فرآیند، قالب به آرامی روی محورهای خود چرخش میکند. از جاذبه هم برای چسباندن پلاستیک به دیوارههای داخلی قالب و تنظیم ضخامت مطلوب قطعه استفاده میشود.
در نهایت، قالب از فر خارج میشود و به آرامی خنک میشود تا از تغییر شکل غیرمطلوب قطعه جلوگیری شود. پروسه خنک شدن ممکن است چند دقیقه به طول بیانجامد. پس از آن، ابزار قالب باز میشود و قطعه آماده برای مراحل بعدی تولید خارج میشود.
این متد برای تولید انواع محصولات و قطعات مختلف مورد استفاده قرار میگیرد. برای مثال بطریها و ظروف پلاستیکی لوازم آرایشی بهداشتی و اسباب بازی.
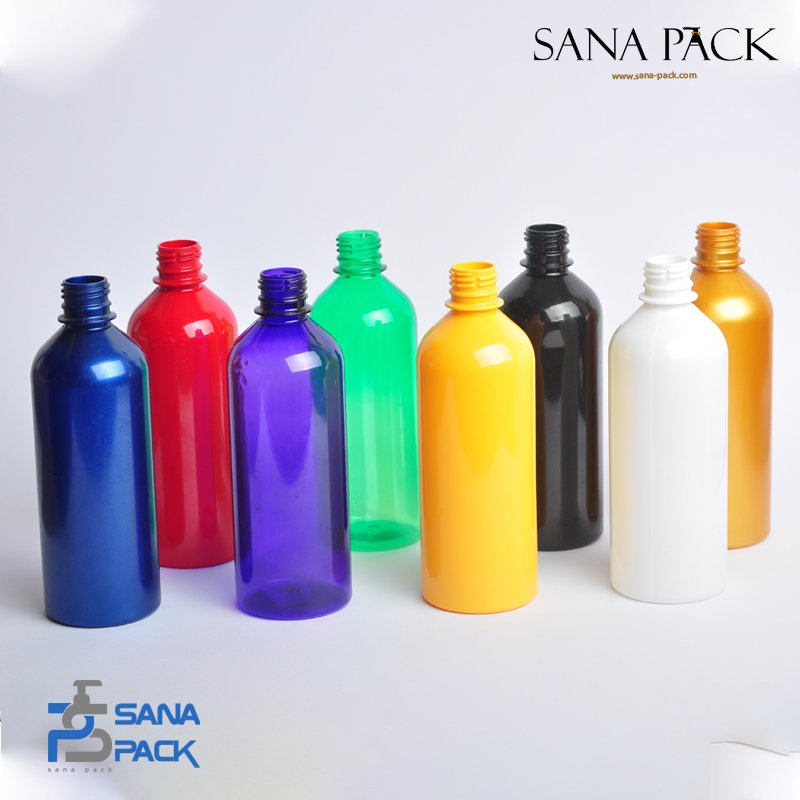
انواع بطری پلاستیکی ثناپک
قالب گیری دمشی اکستروژن( Extrusion Blow Molding)
در پروسه قالبگیری دمشی اکستروژن، پلاستیک مذاب به شکل یک قطره بزرگ به نام پاریزون در داخل یک قالب دو تکه تاشو قرار میگیرد. این فرآیند به این صورت ادامه پیدا میکند:
پس از بستهشدن قالب، پاریزون مانند یک بادکنک باد میشود تا جایی که حفره خالی درون قالب را بهطور کامل پر کند. همچنین، دیوارههای قالب با آب خنک شده و پلاستیک به سرعت جامد میشود. در نهایت، میتوان قطعه جامد را از داخل قالب خارج کرد.
فرآیند قالبگیری دمشی اکستروژن به عنوان یک سیر رایج برای تولید ظروفی با دیوارههای نازک و اقتصادی مورد استفاده قرار میگیرد. نظیر فنجانها و بطریهای یکبار مصرف، سازو کار قالب گیری دمشی اکستروژن سریع و کارآمد است و ابزارهای لازم برای تولید آن به سهولت قابل تهیه و تولید میشوند. با این حال، این سازوکار برای تولید قطعات، پیچیده یا نیازمند دقت بالا مناسب نمیباشد.
قالب گیری دمشی تزریقی(Injection Blow Molding)
قالبگیری دمشی تزریقی یک پروسه تولید پلاستیکی است که در آن از فشار گاز برای فشردن رزین مذاب به داخل حفره قالب استفاده میشود. این فرآیند به راحتی قابل کنترل و تکرار است و معمولاً برای تولید بطریهای پلاستیکی شفاف مورد استفاده قرار میگیرد. این نوع تولید کیفیت سطح بسیار خوبی را ایجاد میکند، اما برای دیوارههای نازک مناسب نمیباشد.
سادگی و کارآیی بالا از ویژگی های قالبگیری دمشی تزریقی هستند.مواد پت (پلی اتیلن ترفتالات) و PEEK (پلی اتر اتر کتون) به دلیل شفافیت و دوام آنها و نیز به عنوان گزینههای ایمن برای مصارف مواد مصرفی، برای تولید بطریهای لوازم آرایشی, بهداشتی و نوشیدنی بسیار مناسب هستند و به راحتی قابل بازیافت هستند.
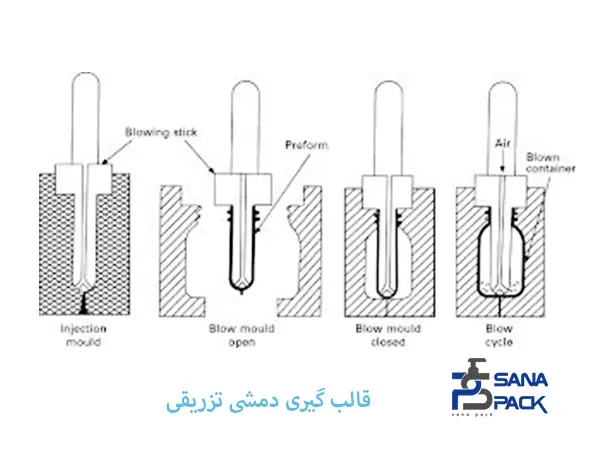
قالب گیری تزریقی واکنشی (Reaction Injection Molding(RIM))
قالبگیری تزریقی واکنش (RIM) یک روند تولید پلاستیک است که به طور گسترده در صنعت خودرو استفاده میشود. این روش قطعات سبک و مقاوم با پوسته سفت تولید میکند، که به طور معمول برای تولید پانلهای بدنه، داشبورد، و قطعات دیگر خودروها استفاده میشود. با این حال، در این روش، پلاستیکهای ترموفرمینگ معمولاً کارایی ندارند، بلکه به پلاستیکهای گرماسخت نیاز دارد.
پلاستیکهای ترموست واکنشهای شیمیایی غیرقابل بازگشتی داخل قالب انجام میدهند، که معمولاً به پر کردن حفرههای قالب منجر میشود. پس از اتمام واکنش شیمیایی، پلاستیک به شکل نهایی خود میآید.
ریخته گری در خلاء(Vacuum casting)
ریختهگری در خلاء یک روش تولید پلاستیک است که برای تولید نمونههای اولیه با کیفیت بالا و تعداد کم بدون نیاز به سرمایهگذاری بزرگ در ابزار یا مواد مناسب استفاده میشود.
در این پروسه، یک مدل اصلی سخت (معمولاً از یک الگوی چاپ سهبعدی) در یک جعبه مهر و موم شده قرار میگیرد و سپس با مواد انعطافپذیر مانند یورتان یا سیلیکون پر میشود. پس از خارج کردن مدل اصلی، یک حفره در داخل قالب به وجود میآید که میتوان آن را با رزین پلاستیک پر کرد تا یک کپی از نمونه اصلی تولید شود. فشار خلاء برای حذف هوا از داخل قالب استفاده میشود تا از وجود حبابهای هوا جلوگیری شود.
این متد دارای توانایی تولید قطعات با کیفیت بالا و جزئیات دقیق است و میتواند بسیاری از مواد مهندسی پلاستیک را شبیهسازی کند. در ریختهگری خلاء، رزینها با واکنش شیمیایی به یک عامل سختکننده جامد تبدیل میشوند به جای اینکه با سرد شدن تغییر کنند.
مزایا این نوع قالب گیری شامل سرعت بالا، سرمایهگذاری ابتدایی کمتر، و تولید نسخههای مشابهی با وفاداری بالا است. اما معایب آن شامل شکنندگی ابزارها و نیاز به جایگزینی آنها بعد از تولید تعداد محدود قطعات میشود.
ترموفرمینگ (Thermoforming)
سازو کار شکلدهی خلاء به این شکل است که در آن یک ورق پلاستیکی نازک یا ضخیم روی یک قالب قرار میگیرد و سپس تحت دمای بالا گرم میشود تا مواد انعطافپذیر شوند، سپس با فشار خلاء ورق را به سمت قالب کشیده میشود تا شکل نهایی خود را بهدست آورد.
پروسه ترموفرمینگ با قالبهای ساده و تجهیزات ابتدایی انجام میشود و بیشتر برای تولید نمونههای اولیه قطعات با دیوارههای نازک و توخالی استفاده میشود. در صنایع مختلف، از شکلدهی خلاء برای تولید لیوانها، دربها، جعبهها، بستهبندیهای پلاستیکی تاشو، و قطعات بدنه خودروها با مواد ضخیمتر استفاده میشود. تنها پلاستیکهای ترموفرمینگ برای این جریان مناسب هستند و ترموستها مناسب نیستند، زیرا مواد باید تحت حرارت نرم شوند و پس از سرد شدن مجدداً سفت شوند.
مزایای این متد شامل مقرون به صرفه بودن و سادگی تجهیزات است و بهویژه برای مدلسازی و تولید نمونههای اولیه مناسب است. همچنین ایمنی این پروسه بالاست زیرا از مواد شیمیایی خطرناک یا دمای بالا استفاده نمیکند.
با این حال، این سازوکار فقط برای ساخت اشکال ساده مناسب است و برای اشکالی با دقت بالا قابل استفاده نیست. همچنین، نیازمند ورقهای نسبتاً نازک است، اگرچه میتوان ورقها را پس از شکلدهی با یکدیگر لمینت کرد تا مقاومت بیشتری ایجاد شود.
در نتیجه همانطور که در بالا اشاره شد روش های ساخت پلاستیک شامل انواع قالب گیری، ریخته گری در خلاء، ترموفرمینگ و… میشوند .در مقاله فوق توضیحات مختصری در رابطه با انواع روش های ساخت محصولات پلاستیکی داده شد. ناگفته نماند که هر یک از این متد ها نیاز به مطالعه ی بیشتر دارند تا انتخاب درستی انجام شود.